射出成形の不良「ヒケ」「ボイド」「バリ」の発生原因と対策
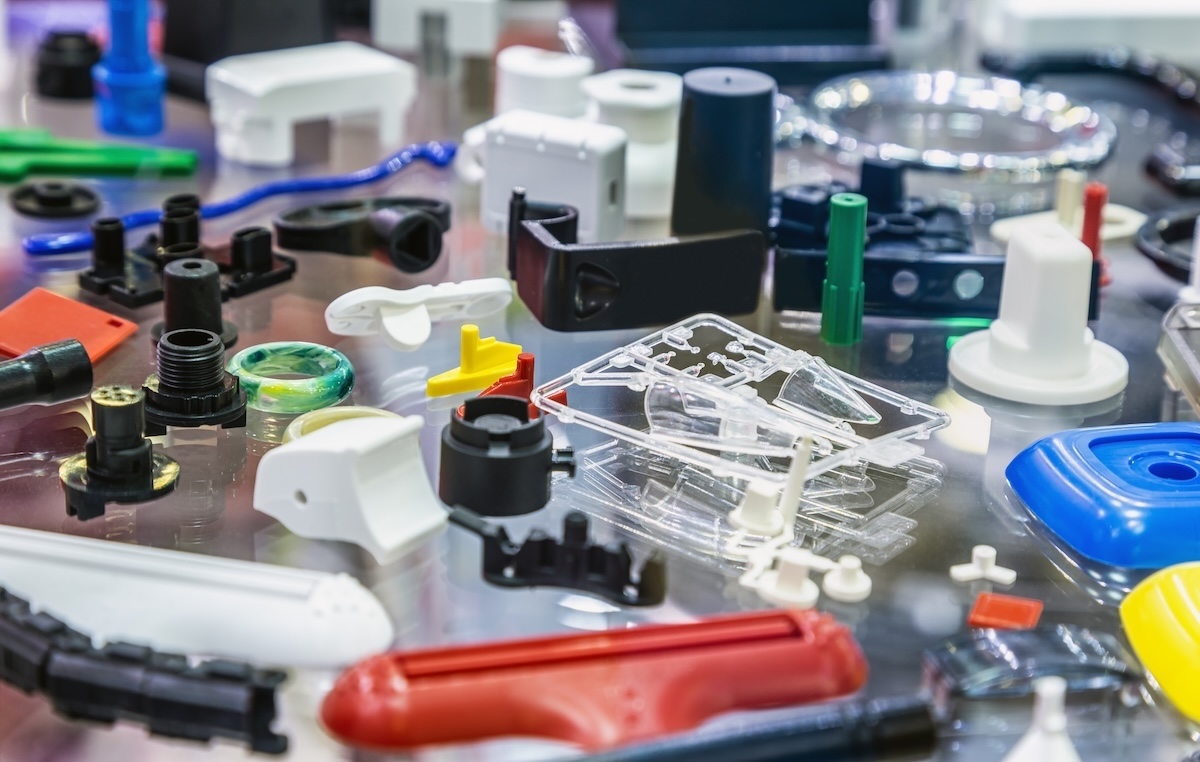
合成樹脂(プラスチック)を原料にした製品の加工法である射出成形において、製造現場における課題のひとつに「成形不良」があります。成形不良はさまざまな要因が複雑に絡み合って起こりますが、成形機での成形条件の調整や、金型設計による対策が可能です。
この記事では、射出成形における代表的な成形不良「ヒケ」「ボイド」「バリ」の原因と対策について、とくに合成樹脂(プラスチック)製品開発に携わる事業者様や設計者様にお役立ていただける基本的な知識をご紹介します。
射出成形不良『ヒケ』
射出成形不良『ヒケ』とは
「ヒケ」は、 射出成形で合成樹脂を加工した際に成形品の表面が凹む現象です。とくに、肉厚が局部的に厚い箇所や、金型温度が局部的に高い箇所で発生しやすい成形不良です。
ヒケは、リブのある反対面 (図a)、ボスの内径 (図b)、厚肉成形品の表面 (図c) などに発生します。
【リブ】
プラスチック部品の強度や剛性を向上させるために設けられる縦横に走る突起。直方体の凸部形状である。
【ボス】
基板や部品を支え、部品の強度を向上させるためにプラスチック部品に追加される突起。ネジなどを収容する穴を備えた円柱や円筒のような形状である。
射出成形不良『ヒケ』の障害
ヒケがあることで外観不良となり、商品価値が失われてしまいます。とくに、塗装やメッキなどの処理を施すとヒケが目立ちやすくなります。圧入やネジ締結の場合はボスなどの内径面がヒケると強度不足になり、レンズのような成形品は球面精度が得られないなど、機能に支障をきたすこともあります。
発生原因とその対策
ヒケの発生メカニズム
肉厚の違いによる、収縮率の差によって成形品の表面が凹む
射出成形は、熱して溶かした樹脂を金型に射出し、型内で冷やし固める成形方法です。キャビティー(金型の凹側の部分)中で熱した溶融樹脂は膨張しており、冷却する際に型内で体積が収縮します。この時、板厚の異なる箇所で収縮分を保圧によって補うことができないと、成形品の表面が内側に向かって引っ張られて生じる収縮率の差が原因となり、ヒケが発生します。
以下に、成形条件・金型・材料・形状ごとにヒケが発生する原因と代表的な対策をまとめました。
推定原因 | 代表的な対策 | |
---|---|---|
成形条件 |
|
|
|
|
|
|
|
|
|
|
|
|
|
|
金型
|
|
|
|
|
|
|
|
|
材料
|
|
|
|
|
|
|
|
|
形状
|
|
|
|
|
|
|
|
射出成形不良『ボイド』
射出成形不良『ボイド』とは
「ボイド」は、成形品の内部に空気の泡が発生する現象です。大きな気泡が発生する「真空ボイド」(図1)と、細かい気泡が多数発生する「マイクロボイド」(図2)があります。
射出成形不良『ボイド』の障害
寸法ばらつきが多い成形品は、ボイドが隠れていることがよくあります。透明な材料の場合は気泡が発生していると外観不良となり商品価値が失われ、不透明な成形品でも内部に気泡があることで強度の低下や破壊の原因になることがあります。
発生原因とその対策
ボイドの発生メカニズム
樹脂の収縮率と温度の関係によって成形品の内部に空気の泡が発生する
成形品肉厚部の中心は成形品の表面に比べて冷却が遅れるため、中心部が溶融している状態で表面から固化していきます。このとき、早く冷えることで収縮の発生が早くなる表面の方向に、樹脂が引き寄せられますが、表面の強度が体積収縮により内部に引っ張られる力より強くなって中心部に空洞が生じることで、気泡として製品内に残ってしまいます。これにより「真空ボイド」が発生します。
また、材料中の揮発成分やシリンダー中の材料の分解によるガスがキャビティー内に充填された際、計量時の圧力から解放されることがあります。これにより「マイクロボイド」が発生します。
これらを防ぐには、金型や樹脂の温度を上げる、保圧を上げる、保圧時間を長くするなどして、成形品の外側と内側の冷却速度の差を縮める対策が有効です。
以下に、成形条件・金型・材料・形状ごとにボイドが発生する原因と代表的な対策をまとめました。
推定原因 |
代表的な対策
|
|
---|---|---|
成形条件 |
|
|
|
|
|
|
|
|
|
|
|
|
|
|
金型
|
|
|
|
|
|
|
|
|
材料
|
|
|
|
|
|
|
|
|
形状 |
|
|
|
|
|
|
|
射出成形不良『バリ』
射出成形不良『バリ』とは
「バリ」は、金型の合わせ面の隙間や突き出しピンなどの隙間に入り込んだ溶融樹脂が溢れて薄い樹脂の膜ができる現象です。バリには、金型の隙間に樹脂が流れ込んで形成されるものと、金型製品部に持ち込まれたガスが抜ける途中に固化して形成されるものがあります。
射出成形不良『バリ』の障害
プラスチックがはみ出すことで成形品の形状に意図しない突起ができて外観不良となるだけではなく、仕上げにバリを除去する工程が増えるためコストが余計にかかります。
さらに、バリの除去を行った箇所にキズが発生すると、そこに衝撃が加わることで簡単に破損してしまう場合があります。発生する箇所によっては寸法バラツキの原因にもなります。
機能部品に見られる代表的な障害
エンジン、ミッション系部品・・・・・バリが脱落した際に潤滑油のダストとして捉えられる
モーターインシュレータ・・・・・・・巻線の絶縁被膜を損傷する
パッキンを装着するもの・・・・・・・パッキンを傷つけシール不良となる
ブラシホルダー ・・・・・・・・・・・ブラシが噛みこみ、モーターが回転しなくなる
ユーザーが触れるもの・・・・・・・・切り傷を負うとPL法に抵触する
その他機能部品・・・・・・・・・・・バリが引っかかり作動不良を起こす
発生原因とその対策
バリの発生メカニズム
金型の合わせ面の隙間や突き出しピンなどの隙間から樹脂が溢れてしまう
バリの発生には、樹脂の流動性が強く関係します。
非結晶樹脂・・・比較的粘度の高い材料が多く、バリが発生しにくいグレードが多い。
結晶性樹脂・・・融点以上では粘度が低下するため、バリが発生しやすい。
樹脂の流動性が低すぎたり、反対に高すぎたりすると成形不良を引き起こしやすくなりますが、成形品の形状などをもとに流動性を考慮した樹脂の規格を指定することで、不良に繋がっているさまざまな課題の解決につながります。
以下に、成形条件・金型・材料・形状ごとにバリが発生する原因と代表的な対策をまとめました。
推定原因 | 代表的な対策 | |
---|---|---|
成形条件 |
|
|
|
|
|
|
|
|
|
|
|
|
|
|
金型 |
|
|
|
|
|
|
|
|
材料 |
|
|
|
|
|
|
|
|
形状 |
|
|
|
|
|
|
|
日邦産業の強み〜流動解析を利用した不良発生箇所の推定と対策〜
射出成形で成形不良が発生し、問題対策のために金型の設計を見直したり、製品形状の修正を繰り返すことで開発期間の延長やコストが増えてしまうといったお困りごとはございませんか?
日邦産業は、CAD(コンピュータを用いた設計ツール)と高度に連携したCAE(流動解析などでCADで作成した設計図に問題がないかを解析できるツール)、3Dデータの効果的な活用によって、試作時に成形不良の事前予測を行います。
さらに、金型設計の技術と応用的な射出成形のノウハウに基づいて成形不良の対策を講じた樹脂化設計をご提案し、生産性向上を実現させます。
各種解析ツールを利用した、不良モードに対する事前対策をご提案します
成形品のゲート位置と種類は成形不良の発生に大きく影響するため、射出成形において金型内にどのように樹脂を流すかがポイントとなります。そこで、本来は見ることができない金型内の樹脂の流れを解析するためのソフトとして「流動解析」と呼ばれるツールが使用されます。
【流動解析】
製品の設計段階で金型内の樹脂の流れをコンピュータ上でシミュレートし、製品の品質に直結する樹脂の流れ方や充填パターンを予測するCAE(Computer Aided Engineering)解析の一種
流動解析によって以下のようなことが可能となります。
・金型内の樹脂の流れのシミュレーション
・ゲート箇所からの最終充填までの樹脂の流れを可視化できる
・不良が発生する箇所の推定
・ウェルド箇所、ガラス繊維の配向、最終充填箇所を可視化できる
流動解析によって樹脂の流れや充填過程を可視化することで、流動パターン・樹脂圧力分布・樹脂温度分などが分かります。その結果から、ヒケの発生位置と深さの予測や、バリ・異物・接点・割れ・欠品等、ウェルドラインなどの不良発生の可能性を見出すことができるのです。
これらを製品の形状へフィードバックすることで、成形機側での成形条件の調整や製品の形状変更、金型の変更などのご提案が可能となります。ものづくりの最初の段階で事前対策を講じることで、納期短縮やコスト削減にも貢献します。
射出成形における不良にお困りの方や、成形品質の改善、生産性の向上をご希望の方は、製品の構想・設計段階よりお手伝い出来る日邦産業にぜひご相談ください。
射出成形に関するお問い合わせ・試作のご依頼はこちら
日邦産業は、射出成形・成形材料・金型製作に関するお問い合わせを随時受け付けております。ご不明点や記事にはないお困りごとのあるお客様には、個々の状況に応じて最適なご提案をいたします。まずはお気軽にご相談ください。
日邦産業株式会社お問い合わせフォーム