「射出成形」とは?
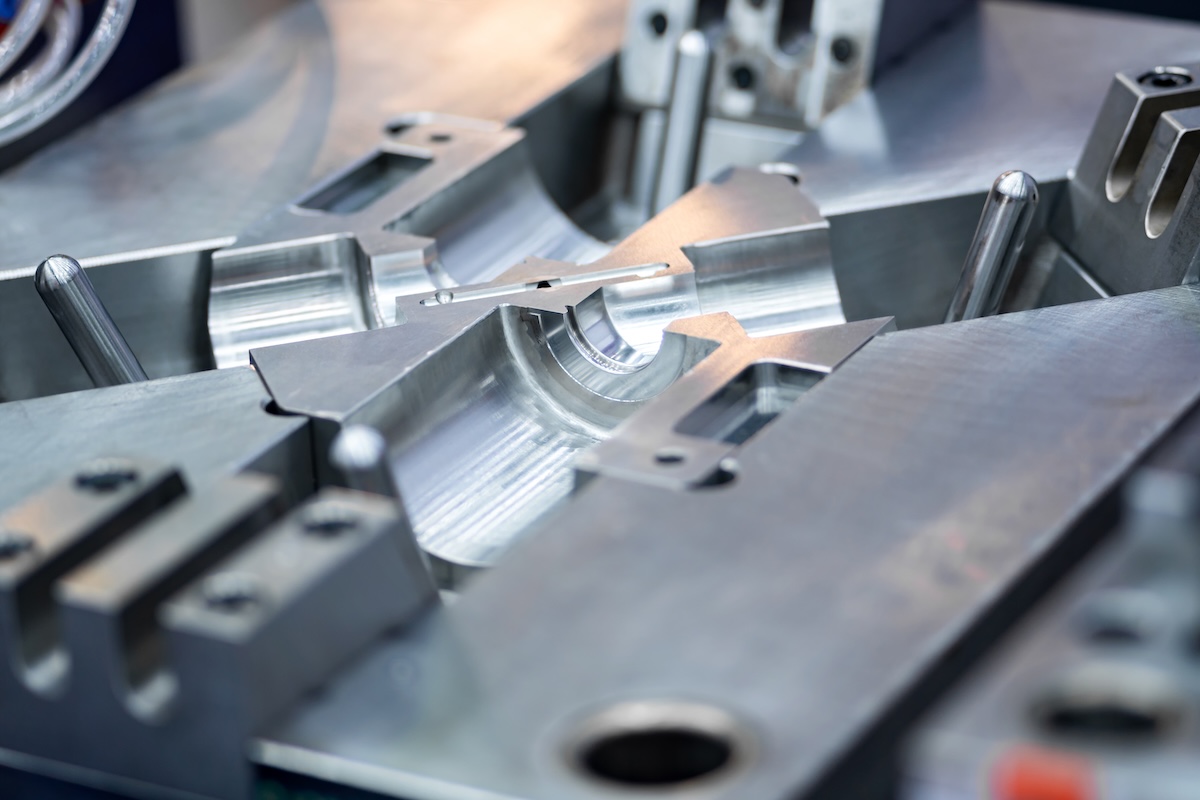
プラスチック製品の加工法には数多くの工法がありますが、その中でも製品の量産に用いられる最もメジャーな加工法が、金型を使った「射出成形」です。私たちの身の回りにある多くのプラスチック製品が、この「射出成形」によって作られております。
当社は、プラスチックの射出成型メーカーとして、長年モノづくりを行ってきました。その経験と知見を活かして、「射出成形」の基本的な知識から製品製造に関する専門情報までをわかりやすくまとめ、【射出成形を知る】シリーズ(全3回)としてご紹介いたします。特にプラスチック製品の開発に携わる事業者様、設計者様にお役立ちいただける情報としてご参考いただけると幸いです。
プラスチックの加工法「射出成形」の特長とは?
「射出成形」とは、射出成形機と呼ばれる機械を使用し、金型内に加熱溶融させたプラスチックを高圧で射出して成形する工法です。複雑な形状の再現性が高く、多様な形の部品を連続して素早く大量に製造することができるという特長があり、日用品をはじめ、家電、自動車、航空宇宙分野など、幅広い分野の製品で利用されています。
射出成形機のしくみ
射出成形に必要な射出成形機は、ペレット(粒状になった樹脂)を溶かす【溶融】、型に流し込む【射出】、固める【冷却】、取り出す、という工程を1台で処理することができる工作機械です。ペレットを溶かして金型の内部に送り込む「射出部」と、金型をセットする「型締部」、成形条件を制御するための「コントローラー」で構成されています。
近年は射出成形機のCNC化(コンピュータを使用し、作成したプログラムに基づいて工作機械を数値制御して行う加工)が進んでおり、射出成形の速度や圧力、シリンダー温度、金型温度、材料の射出量などの成形条件を指定して制御することで高精度の成形品を安定して生産可能な機種が普及しています。
射出成形のステップ
加工の流れとしては、樹脂製品の材料となるペレットを射出成形機に流し込み、「溶かす」「充填する」「固める」「取り出す」という工程が基本です。
<STEP 1>
ホッパーにペレットを投入します。
<STEP 2>
スクリューを回転させ、その剪断熱(スクリューにより材料を圧縮する際に発生する熱)と外部ヒーターの熱により、ペレットをシリンダー内で水飴状に溶かします。
<STEP 3>
スクリューを前進させ、金型の中に水飴状に溶かしたペレットを射出します。
<STEP 4>
冷却された金型に保持する事で、水飴状のペレットを固化させます。
<STEP 5>
金型を開き、エジェクタ機構により製品を金型から突き出します。
一般の射出成形では、以上の工程を自動で一定時間内に繰り返す事で、同じ形状の製品を大量に生産する事が可能です。
日邦産業の強み 〜成形プラスαの一体化技術〜
日邦産業は単品部品成形だけでなく、一体化技術による複合部品の製造を得意としています。
<事例1>部品一体化の技術とそのご提案
従来工法では平歯車+ウォーム+シャフトを別で製造し、後で組立していましたが、それを一体成形させる事で組み立て上の問題(抜け強度等)の解決と組立て工程の削減によるコストダウンを実現します。
<事例2>封止インサート技術(金属⇔樹脂 シール(密着)技術)
通常のインサート成形では、金属と樹脂を密着させることができず完全シールができません。そのため、特殊工程を追加させて完全シールを行う当社の独自(PAT.)技術です。
一般的に樹脂と金属の界面は密着しておらずシール性は確保できていないため、電気的絶縁や部材腐食の要因となることが多く、このような当社独自の工法により高度なシール性が確保でき冷熱試験による熱応力に対しても有効です。
射出成形の短納期試作でお悩みの加工メーカー様へ
当社では、独自の射出成形による高速試作でお悩みを解決します!。
「射出成形による高速試作」のご紹介はこちら金型製作・試作対応の流れ
各社エンプラ樹脂素材とインサート金属種の中から、お客様のご要望に合わせた部材と表面処理、メッキの選定、製品の形状提案、金型製作、生産まで可能です。
まずは一度お問い合わせください。
射出成形に関するお問い合わせ・試作のご依頼はこちら
お客様のご要望に合わせた構造・機構設計を承ります。必要なサイズ、機能、特性などの情報を基に、最適な設計仕様をご提案させていただきます。
日邦産業株式会社お問い合わせフォーム
国内3拠点に加え、アセアン(タイ・マレーシア・ベトナム・インドネシア・フィリピン)に生産拠点を構え、グループ内で展開されたモノづくりノウハウにより、高品質な製品をご提供しております。