射出成形における「成形不良」発生の原因と対策まとめ
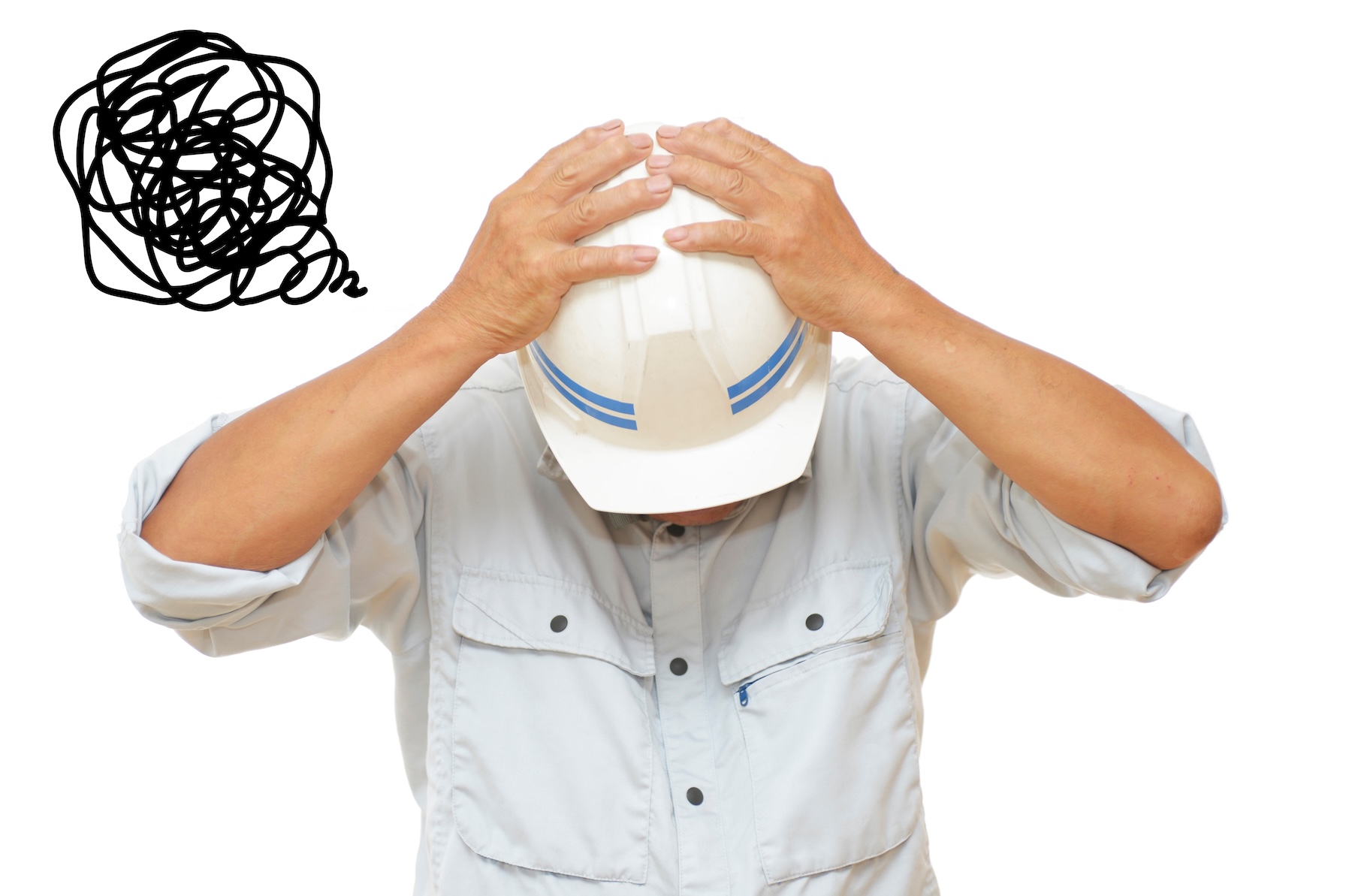
射出成形における「成形不良」にお困りではありませんか?生産性の向上やコスト削減を実現するためには、成形不良の対策を把握して不良率を削減することが重要です。
この記事では、射出成形における代表的な成形不良の種類とその発生原因、金型設計や成形機での成形条件の調整によって可能な対策についてまとめました。
成形不良でお悩みの方や、今後成形不良品ゼロを目指したい方にお役立ていただける基本的な知識を中心にご紹介します。
射出成形不良とは
成形不良とは、射出成形によって成形されるプラスチック製品の表面の欠陥や割れ、歪み、収縮、気泡などのように、成形品の外観や性能上に不具合が発生する事象を指します。
これらの成形不良は、樹脂の素材や、射出成形時の速度・温度・湿度・圧力といった成形条件、金型の設計・状態、機械の調整などのさまざまな要因が引き金となって発生します。
主な射出成形不良の原因と対策
成形不良といってもさまざまな種類がありますが、主に成形条件・材料・製品形状・成形機や金型が起因しており、成形不良の種類によって有効な対策が異なります。
以下に、主な成形不良の原因とその対策を簡潔にまとめました。
ヒケ
ヒケとは、成形品の表面が部分的に凹状になる現象です。肉厚が局部的に厚い箇所や、金型温度が局部的に高い箇所で発生しやすい不良です。
【原因】
溶融樹脂が固化する際に、通常はキャビティー(金型の製品形状の部分)で起こる体積収縮を保圧によって補う必要があります。
しかし、内部が固まり切らない内に保圧が効かなくなると、金型表面に接して既に固化している表面が内部の収縮により内側に引っ張られ、凹状になります。
【対策】
溶融樹脂と金型の温度を低く設定することで成形品表面を速く固化させるか、金型の温度を上げてゲート部の固化を遅くすることで、ヒケの発生を防ぐことができます。
また、ヒケ発生箇所に肉盗みを設置し、製品肉厚を均等にすることも有効な対策です。
成形条件・金型・材料・形状ごとにヒケが発生する原因と対策は異なります。
ボイド
ボイドとは、成形品の内部にエアーが発生して空洞が出来る現象です。
大きな気泡が発生する「真空ボイド」と、細かい気泡が多数発生する「マイクロボイド」の2種類に分かれます。ボイドは外観だけでなく、成形品の強度低下など品質にも影響します。
【原因】
「真空ボイド」は樹脂が金型内で固化するする際、固化した部分の強度が固化していない内部の収縮力より強いと、内側の部分がそれ以上収縮出来なくなり、内側に真空の空洞を作ってしまう現象です。
「マイクロボイド」は、材料中に含まれる揮発成分のガスや計量時にシリンダー内で巻き込まれた空気の粒が、キャビティー(金型の製品形状部)内に樹脂と一緒に流れ込んで、製品内に空気の粒が発生する現象です。
【対策】
金型や樹脂の温度を上げる、保圧を上げる、保圧時間を長くするなどして、成形品の外側と内側の冷却速度の差を縮める対策が有効です。
成形条件・金型・材料・形状ごとにボイドが発生する原因と対策は異なります。
バリ
バリとは、金型のパーティング面(合わせ面)やスライド、入れ子の隙間に溶融樹脂が入り込み、金型からはみ出したような状態で凝固して薄い樹脂の膜が出来る現象です。
金型の隙間に樹脂が流れ込みバリになる場合と、金型製品部に持ち込まれたガスが抜ける途中に固化してバリになる場合があります。
【原因】
バリの発生には樹脂の流動性が強く関係します。とくに流動性が高い材料に対しては、成形条件として射出速度や圧力を上げ過ぎることで発生します。
金型条件としては、その構造はもちろんですが、剛性不足や入れ子の合わせ不足が原因となり発生します。
【対策】
成形条件では、射出圧力や速度を下げて、低圧成形を行うという対策が有効です。金型条件では、入れ子の隙間をなくし、剛性を上げて金型が歪まないようにする対策が有効です。
成形条件・金型・材料・形状ごとにバリが発生する原因と対策は異なります。
ウェルドライン
ウェルドラインとは、金型内部を流動する成形材料の樹脂が金型内を分岐した後に、キャビティー(金型の凹側の部分)内で再び合流する箇所にV字型の溝が発生する現象です。
【原因】
樹脂が分岐して流れていく過程で温度が下がっていきます。分岐後に再び合流する際、樹脂の先端部分の凝固した樹脂がぶつかり合った部分に溝が生じることで発生します。
【対策】
主に成形条件では、速度や圧力を高める対策が有効です。また、金型の温度や樹脂の温度を上げることにも同様の効果があります。金型では、ゲート位置の変更や樹脂の流れる面積を大きくし、流動抵抗を下げるという工夫も効果があります。
成形条件・金型・材料・形状ごとにウェルドラインが発生する原因と対策は異なります。
ショートショット
ショートショットとは、溶融樹脂が金型内に充填されていない状態で凝固してしまい成形品の一部が欠けてしまう現象です。ゲートから遠いところに位置している箇所が欠けやすくなります。
【原因】
ショートショットは、樹脂の不足や流動性の悪さなど材料に起因するもののほか、金型の温度が低すぎる、射出の圧力が不足しているなど成形時の条件が原因となることがあります。また、成形品に肉厚差がある場合もショートショットが発生しやすくなります。
通常、金型内を流れる樹脂は充填しやすい肉厚部から充填されて、次に薄肉部に樹脂が充填されますが、成形品に肉厚差がある場合、薄肉部は少し入ったところで流動性が落ちて凝固し始めます。
そのため、十分な射出圧力がかかりにくくなり、製品の末端まで樹脂が充填されないという問題が発生します。
エアー逃げの悪い成形品形状や精密金型でパーティング面(金型が分割される面)の精度が高い場合も、押し込められたガスの圧力で末充填になることがあります。
【対策】
とくに高速充填では、エアーが逃げきらないうちに充填されるため末充填になりやすいため、エアーベント(金型内に充填される樹脂の際に発生するガスやエアー、圧縮されたエアーを金型外に排出する溝や穴)を設置する対策が必要です。
キャビティの真空引き(金型内に残留するエアーを吸引して除去し、金型密閉度を向上させる事前加工)を行う、樹脂の固化を防ぐために成形温度を上げる、射出速度をあげて保圧時間を伸ばすといった方法もあります。
成形条件・金型・材料・形状ごとにショートショットが発生する原因と対策は異なります。
シルバーストリーク
シルバーストリークとは、成形品の表面に樹脂が流れる方向に合わせて銀白状の筋が発生する現象です。
【原因】
発生原因は大きく3つに分類されます。
①材料に含まれる水分
射出成形の中で、材料として熱可塑性樹脂(加熱すると溶けて軟化し、冷却すると固化する特性を持つプラスチック)を使用する場合、材料中の水分を十分に乾燥しておかないと、その水分に材料が反応してシルバーストリークが発生します。
また、成形機のシリンダー(成形材料を入れて加熱するための筒)内の水分や揮発分などの脱気不良も原因となります。
②金型の形状
使用する金型が、成形時に発生するガスやエアーを適切に排出できる形状になっていないと、スクリューの回転や射出工程で型に巻き込まれるエアーなどが充填過程でつぶれて、シルバーストリークとなって成形品表面に現れます。
③金型とシリンダーの温度
金型やシリンダーの温度が低すぎると樹脂の流動性が低下し、金型の内部を均一に流れることが難しくなってシルバーストリークが現れます。
シリンダーの温度が高すぎると、樹脂からガスが発生してシルバーストリークになる可能性があります。また、滞留焼け(成形機のシリンダー内に残っていた樹脂が焼けて炭化してしまうこと)も原因となります。
【対策】
成形材料の乾燥を十分に行い溶融樹脂内にエアーが混入しないようにすること、材料のプラスチック樹脂だけでなく金型にも水分が付着していないか注意しておく必要があります。
また、射出成形時はガスが発生するため、ガスや空気を逃す通り道として金型内にガスベント(エアベント)を適切に設計する対策も有効です。
成形条件・金型・材料・形状ごとにシルバーストリークが発生する原因と対策は異なります。
※シルバーストリークの詳細は順次公開予定です
フローマーク
フローマークとは、成形品のコーナー部や凸凹部などに発生する白雲上の外観をした模様のことです。一旦キャビティー(金型の製品形状の部分)の表面に固化した樹脂の層が再流動した時に発生します。
【原因】
金型に充填された溶融樹脂は金型の表面に接触した箇所から冷えていきますが、温度が低い場合や速度が遅い場合に、樹脂の先端部で温度差が生じます。
この時、樹脂の流動性が下がって充填速度が変化し、一定の速度で流れていかないことでフローマークが発生しやすくなります。
【対策】
溶融樹脂が一定の速度で流れるように、樹脂の温度を上げると同時に金型内部の温度を上げること、また射出速度を上げると同時に射出圧力を高めることが有効です。
成形条件・金型・材料・形状ごとにフローマークが発生する原因と対策は異なります。
※フローマークの詳細は順次公開予定です
ガス焼け
ガス焼けとは、金型に樹脂が射出されている際に過剰に加熱され、成形品全体が茶褐色になってしまったり、ゲート部分から流れ方向に向かって茶褐色のスジが発生する現象です。
【原因】
成形品に樹脂の流れが悪い箇所があり、その部分に金型内の空気や成形材料から発生するガスが滞留・圧縮されて樹脂が高温になってしまうことで発生します。
また、成形機のシリンダーやノズルが高温になっている場合や、滞留時間が長すぎる場合にも樹脂が分解しガスが発生するため、ガス焼けが発生し易くなります。
【対策】
射出圧力が強すぎないように適切な圧力に調整する必要があります。温度や射出速度・圧力を下げたり、ガスベントの設置や型内構造の見直しが必要です。
成形条件・金型・材料・形状ごとにガス焼けが発生する原因と対策は異なります。
※ガス焼けの詳細は順次公開予定です
異物不良
異物不良は、①黒点異物②金属異物③樹脂異物の3つに分類されます。
①黒点異物
樹脂が熱分解して炭化することで発生した黒色の異物が、成形品に練り込まれた状態のものを指します。
②金属異物
成形機や周辺装置の劣化や部品の脱落など、インサートの表面部剥離が原因で発生します。金属片は加熱された樹脂と一緒に混ざり、成形品に充填されてしまいます。
③樹脂異物
乾燥機やホッパーなどで混入することが多く、強度不良、層状剥離、色ムラなどが発生します。
【原因】
①黒点異物
材料の保管中にほこりや異物が混入したり、原材料自体に異物が含まれることが原因となります。
②金属異物
成形機や周辺装置の経年劣化や、機械の振動などにより部品が脱落してしまうことが原因です。とくに粉砕材料を使用している場合は、粉砕機内の脱落に注意が必要です。
また、インサート成形の場合、インサートの表面が剥離して金属異物になる場合もあります。
③樹脂異物
清掃不足により、前に生産していたペレットが混入することが原因です。まれに、隣のライ ンで生産していたペレットが飛んで混入することもあります。
【対策】
①黒点異物
原料にゴミが練り込まれていないか成形前に確認し、ごみを除去した状態で使用するようにしましょう。また、シリンダー(材料の加熱や冷却の温度制御を行う部分)を分解して清掃することも大切です。
②金属異物
インサート成形の場合、プレス品の返りバリやメッキ粕が欠け落ち混入することがあります。機械装置の日常点検を徹底し、部品の品質を上げることと、粕はけの良い金型作りや成形ショット毎のエアーブローなどが必要です。
③樹脂異物
成形ライン内の掃除が行き届いていないと、段取り替え前のペレットが残ったまま混入してしまう恐れがあります。スクリュー(材料の加熱から押し出しまでを行う部分)などを分解して清掃することが必要です。
成形条件・金型・材料・形状ごとに異物不良が発生する原因と対策は異なります。
※異物不良の詳細は順次公開予定です
光沢不良
光沢不良とは、成形品の表面で光沢が失われたり、細かいブツが発生する現象です。
【原因】
材料からガスが発生することでキャビティ面の転写が悪くなる場合と、金型温度が低すぎるためキャビティ面の転写が悪い場合があります。
【対策】
樹脂温度や滞留時間といった成形条件、ガスペイントなどの型設計対策が重要です。
※光沢不良の詳細は順次公開予定です
層状剥離
層状剥離とは、成形品の表面で層状に剥離する現象です。
【原因】
キャビティ(金型の製品形状の部分)の中を樹脂が流れる場合、表面の固化層と内部の流動層の間でせん断力を受けて配向が起こりますが、この配向層のところで剥離が起こると考えられます。
うまく溶け合わない樹脂同士が混ざってしまった時や、樹脂・金型の温度が低すぎるなど、成形条件が不適正である時に発生します。
【対策】
射出速度を落とす、製品形状の肉厚を厚くするという対策が有効です。また、材料要因では、相溶性を向上させる添加剤を加える等も効果的です。
成形条件・金型・材料・形状ごとに層状剥離が発生する原因と対策は異なります。
※層状剥離の詳細は順次公開予定です
湯ジワ
湯ジワとは、成形品の流動末端近くに発生するさざ波状のシワ模様のことです。
【原因】
フローフロント(樹脂が金型内を流動する際に湧出る箇所)の先端が冷えて温度差が生じることで充填速度が変化することで発生します。
【対策】
樹脂の流動性を良くしたり、成形温度や射出速度を上げるという対策があります。
成形条件・金型・材料・形状ごとに湯ジワが発生する原因と対策は異なります。
※湯ジワの詳細は順次公開予定です
射出成形のご相談・成形不良の改善なら日邦産業へ
射出成形において、成形不良を防ぐための適切な成形条件は、樹脂の種類や金型の構造などによっても変化します。成形不良を解消するためには不具合を予測し、不良の原因となるものをしっかりと見極めて対応していく必要があります。
日邦産業では、成形不良の対策のカギとなる金型の精度の高さにこだわり、金型の設計から製作、成形まで一貫して対応いたします。また、成形不良対策としての金型変更もお気軽にご相談ください。
さらに、各種解析ツールを用いた成形不良の事前予測に基づいて製品形状へフィードバックすることで、射出成形の成形不良の解消と品質向上、コスト低減、生産性の向上など幅広いテーマで貢献します。
成形現場でのお困りごとや、成形品質の改善、生産性の向上については、製品の構想設計段階よりお手伝い出来る日邦産業にぜひご相談ください。
射出成形に関するお問い合わせ・試作のご依頼はこちら
日邦産業は、射出成形・成形材料・金型製作に関するお問い合わせを随時受け付けております。ご不明点や記事にはないお困りごとのあるお客様には、個々の状況に応じて最適なご提案をいたします。まずはお気軽にご相談ください。
日邦産業株式会社お問い合わせフォーム